55 Conseils et meilleures pratiques de préparation de commandes d'entrepôt d'experts
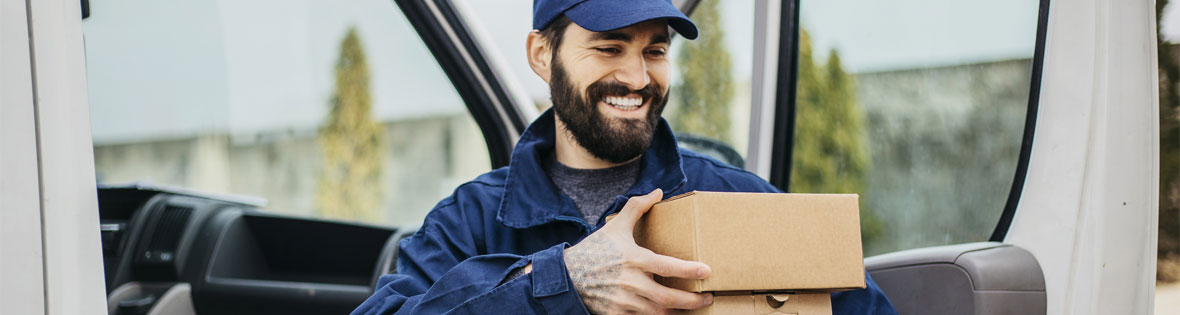
Il existe de nombreux processus entrants et sortants impliqués dans le déplacement et la gestion des stocks qui constituent la discipline de la gestion des entrepôts. Les entreprises se concentrent souvent sur les processus sortants pour augmenter la satisfaction des clients et réduire les inefficacités et les coûts opérationnels.
Mais la préparation des commandes est une partie cruciale de la gestion des entrepôts sortants. Il constitue l'ensemble des étapes de récupération physique des articles stockés dans l'entrepôt pour répondre à une commande client.
Importance d'améliorer la préparation des commandes dans l'entrepôt
Les entreprises intelligentes cherchent à améliorer la préparation des commandes pour une bonne raison :c'est l'activité la plus laborieuse et la plus chère de l'entrepôt, représentant généralement plus de la moitié des coûts d'exploitation de l'entrepôt.
Les améliorations apportées à la préparation des commandes aident les entreprises à fournir plus rapidement les bons produits aux clients, et dépenser moins d'argent sur les étapes associées. Les sélecteurs de commandes d'entrepôt prennent généralement une liste de sélection et se rendent à différents endroits de l'entrepôt pour obtenir les articles, les rechercher sur les étagères de l'entrepôt, extrayez-les et faites correspondre les documents pour assurer l'exactitude de la commande avant l'expédition.
La partie la plus chronophage du processus de préparation des commandes est le déplacement, qui occupe 55% du temps du sélectionneur d'entrepôt, en moyenne, suivi de la paperasse et d'autres activités (20 %), recherche (15%) et extraction (10%), selon les recherches du Georgia Tech Supply Chain and Logistics Institute. Pour cette raison, une grande partie du travail d'amélioration des processus de préparation des commandes vise à réduire les temps de déplacement improductifs.
Pour obtenir la meilleure préparation de commandes de sa catégorie, il faut savoir où se trouvent les produits, combien sont disponibles exactement, en sachant combien vous en avez besoin - vous ne prélevez donc pas pour chaque commande individuelle une à la fois - et en vous assurant qu'elles sont stratégiquement placées pour faciliter la cueillette et le traitement rapides pour l'expédition.
Alors, comment les entreprises peuvent-elles minimiser le temps de préparation des commandes tout en garantissant une exécution précise des commandes et la sécurité des employés dans un entrepôt ?
55 conseils de préparation de commandes en entrepôt et meilleures pratiques à adopter
Puisqu'il n'y a pas qu'un seul moyen d'assurer des commandes parfaites, il existe de nombreuses méthodes, outils et processus qu'une entreprise peut utiliser pour améliorer la préparation des commandes. La combinaison de stratégies, les meilleures pratiques et technologies que votre organisation devrait adopter dépendront de l'industrie, nombre d'articles vendus et vitesse à laquelle les stocks se déplacent dans le(s) entrepôt(s).
L'examen de la conception de l'entrepôt et des méthodes de préparation de commandes utilisées dans ses quatre murs aidera une entreprise à sélectionner les processus appropriés, technologies et équipements pour améliorer la préparation des commandes.
Conseils de conception d'entrepôt pour la préparation de commandes
L'excellence de la préparation des commandes commence par le choix de la conception et du flux d'entrepôt adaptés à votre stratégie de processus métier.
-
Choisissez un type d'entrepôt et un flux. Les entrepôts sont généralement conçus pour déplacer des marchandises dans l'une des configurations ci-dessous (ou une combinaison de celles-ci).
- Flux en U positionne les quais de réception et d'expédition du même côté du bâtiment, et les produits se déplacent en forme de U de la réception à l'expédition. Cette conception offre un espace d'amarrage partagé et est généralement la meilleure pour les petits bâtiments.
- Flux en forme de I placez la réception à une extrémité et l'expédition à l'autre extrémité du bâtiment afin que toutes les marchandises se déplacent dans une seule direction. Un flux en forme de I est bon pour les entreprises à volume élevé, ainsi que ceux qui ont besoin d'un contrôle de sécurité strict sur les marchandises entrant et sortant de l'entrepôt.
- Flux d'entrepôt en forme de L a un déchargement entrant à une extrémité et une expédition sortante à un angle perpendiculaire à cette zone. Cela peut faciliter le cross-docking, lorsque les articles sont retirés d'un camion et immédiatement chargés sur un autre. C'est bon pour les entreprises qui peuvent ne jamais stocker de produits sur des étagères, envoyer le stock peu de temps après l'avoir rentré.
-
Décidez comment le produit est organisé au sein de ce flux. Cela pourrait être ce qu'on appelle une conception d'entrepôt triadique, qui est divisé en trois zones - rapide, produit moyen et lent. Dans les entrepôts qui n'utilisent pas cette conception, le produit n'est pas zoné. De nombreux entrepôts adoptent une conception dans laquelle ils automatisent une section avec des articles appropriés tout en ayant toujours des personnes impliquées dans la cueillette des articles, dans une certaine mesure, dans l'autre.
- Placez les produits les plus rapides au plus près de l'exécution afin qu'ils soient faciles à choisir.
- Stockez les articles qui se vendent souvent ensemble les uns à côté des autres.
Méthodes de prélèvement des commandes en entrepôt
Si vous n'avez pas de méthode de cueillette, vous choisirez pour chaque commande de manière chronologique sans visibilité sur les autres commandes de votre file d'attente - cela entraîne une perte de temps considérable à traverser l'entrepôt pour récupérer le même article tout au long de la journée.
-
Les opérations avec un faible volume de commandes ou qui vendent des produits haut de gamme ou lourds doivent se tourner vers la discrétion, prise de commande individuelle, prélèvement de pièces ou préparateur à pièce. C'est la méthode de préparation de commandes la plus simple, dans laquelle une personne prélève la commande complète, traverser l'entrepôt, en tirant tous les éléments nécessaires et souvent en les regroupant dans un conteneur.
-
Pour les organisations qui ont besoin de prélever et d'emballer rapidement des commandes de plusieurs articles et d'avoir un nombre élevé de SKU et de prélèvements par commande, la cueillette des vagues est un bon choix. La cueillette s'effectue par vagues programmées, et toutes les zones sont sélectionnées en même temps. Les articles sont triés en aval au fur et à mesure qu'ils sont préparés pour des expéditions individuelles. Le prélèvement par vague place les commandes ensemble sur la base de règles prédéfinies et les libère pour qu'ils soient exécutés ensemble afin que les préparateurs puissent prélever pour toute la vague en même temps.
-
Pour augmenter l'efficacité de la cueillette, les travailleurs peuvent prélever par lots où ils prélèvent pour plusieurs commandes, telles que des articles similaires ou des articles situés dans des zones similaires, en un seul voyage. Pour les entreprises avec un faible nombre de prélèvements par commande, la cueillette par lots peut réduire le temps de déplacement. L'opérateur entre dans l'entrepôt, sélectionne la quantité totale d'articles requis et les affecte ensuite à chaque commande individuelle.
-
Pour les grands entrepôts avec de nombreuses références, la cueillette de zone est souvent avantageuse. La cueillette par lots peut intégrer la méthode de cueillette par zone, dans lequel un sélectionneur est chargé de s'occuper d'une certaine zone de l'entrepôt, obtenir tous les articles pour leur zone, puis passer la commande. Pour cette raison, la sélection de zone est également connue sous le nom de sélection et de passage. Les objets peuvent bouger, par exemple, le long d'un tapis roulant jusqu'à ce que tous les articles requis soient dans la boîte.
-
Les entreprises innovantes essaient des configurations et des systèmes de tri adaptés aux personnes pour augmenter l'efficacité du processus de prélèvement. Le sélecteur d'entrepôt reste au même endroit, et les produits sont amenés au sélecteur par un convoyeur, un appareil robotique ou une autre technologie automatisée. Considérez le bien-à-personne comme l'automatisation du processus de prélèvement discret.
-
Une autre façon de réduire le temps de trajet est le pick-to-box. Pick-to-box intègre davantage d'automatisation dans le prélèvement par lots. Les zones de picking peuvent être organisées en postes de picking, chacun relié par une bande transporteuse. Le sélectionneur remplit la boîte avec les produits dont il a la charge et déplace la boîte jusqu'à ce que la commande soit exécutée.
Équipement et technologie de préparation de commandes en entrepôt
Un autre aspect clé de la gestion d'entrepôt est la technologie qui prend en charge la stratégie optimale pour l'installation et la nature de l'entreprise. Par exemple, une entreprise avec un petit nombre de SKU et moins de lignes prélevées peut utiliser une méthode de prélèvement de commande individuelle, et tirez parti de la technologie pick-to-belt ou pick from palette. Les entreprises avec un grand nombre de SKU qui déplacent des volumes élevés peuvent opter pour le prélèvement par lots et la technologie vocale ou pick-to-light.
Pour déterminer quels équipements et technologies sont adaptés à votre entrepôt :
-
Alignez la technologie avec le nombre de SKU et le volume. Regardez le nombre de lignes traitées par jour par rapport au nombre de produits. En général, plus le nombre de SKU et le nombre de lignes sont élevés, plus le besoin d'automatisation est grand.
-
Commencez par mettre en place un système de gestion d'entrepôt (WMS). Même les opérations d'entrepôt les plus simples nécessitent une forme de système de gestion d'entrepôt. Recherchez la fonctionnalité de préparation de commandes de base pour stocker et suivre les SKU et l'emplacement des articles et automatiser la création de listes de sélection à partir des commandes des clients. Un WMS vérifiera une commande client par rapport à l'inventaire disponible et fournira des instructions sous la forme d'une liste de sélection. Il prend en compte l'agencement de l'entrepôt, la main-d'œuvre disponible et l'emplacement de l'équipement pour maximiser l'efficacité et assurer la précision de la préparation des commandes.
-
Intégrez une forme de technologie de prélèvement mobile. Des scanners RF mobiles de base, aux technologies qui orientent les sélections en éclairant des boutons sur les étagères dans un chemin de sélection (pick-to-light) ou guident un sélecteur de casque par la voix (pick-to-voice), il existe de nombreuses technologies mobiles indispensables à une préparation de commandes précise, guider les utilisateurs vers l'allée exacte, étagère, ou bin dans le chemin le plus logique. Assurez-vous que les technologies utilisées sur le terrain peuvent facilement communiquer avec le WMS afin de ne pas introduire de complexité inutile.
-
Assurez-vous que le WMS est intégré au système ERP. Le suivi des mouvements et des marchandises dans l'entrepôt fournit une mine de données précieuses pour les autres départements, comme les achats ou le service client. Assurez-vous que ces autres fonctions ont accès aux mêmes données dans le logiciel qu'elles utilisent pour leur travail.
-
Sélectionnez le bon système de manutention des matériaux et ajustez les systèmes au fur et à mesure que les SKU et le volume augmentent. Une augmentation du nombre de SKU nécessite beaucoup plus de logistique dans l'entrepôt. Avec de faibles références et un faible volume, un système de manutention simple comme les chariots élévateurs peuvent le faire, mais à mesure que le volume et la complexité augmentent, l'entreprise aura besoin de plus de mécanisation. L'équipement de manutention est un espace innovant qui tire parti de nombreuses idées et technologies innovantes.
-
Considérez les progrès de l'équipement pour permettre une configuration d'allée étroite. L'optimisation de l'espace disponible dans l'entrepôt offre des avantages au-delà du stockage - cela peut également aider à réduire le temps de déplacement dans le processus de préparation des commandes. Les allées conventionnelles des entrepôts ont une largeur de 12 à 14 pieds. Les allées étroites mesurent généralement de 8 à 10 pieds, mais peut être aussi petit que six pieds. En combinant les bonnes technologies et équipements, les entrepôts peuvent réaliser des gains de préparation de commandes avec des allées plus étroites.
-
Maximisez l'espace de l'entrepôt en utilisant le bon équipement. La technologie des chariots élévateurs s'améliore constamment, et il y a des camions capables de traverser des allées étroites et dans des espaces restreints, comme le chariot élévateur articulé. Amazon utilise des robots qui ressemblent aux aspirateurs Roomba. Ces robots transportent les articles nécessaires des étagères au préparateur et les repoussent dans des endroits restreints lorsque tous les articles sont récupérés.
-
Mettre en œuvre la technologie des convoyeurs. Il existe des dizaines de types de technologies de convoyage qui peuvent être utilisées pour une cueillette plus efficace, ainsi que la santé ergonomique des employés effectuant le travail.
-
Regardez les progrès des technologies de tri. Combiné avec des convoyeurs, les technologies de tri améliorent la précision et l'efficacité — produisant des délais de livraison plus courts et plus de précision.
-
Découvrez quel stockage est adapté à l'entreprise et ne négligez pas les avantages des technologies automatisées. Un carrousel, par exemple, automatise le prélèvement au moyen d'un rayonnage qui tourne le long d'un rail pour amener les articles au préparateur. Ils peuvent être configurés selon le mode de cueillette choisi par l'entreprise.
-
Comprenez toutes les options de technologie de cueillette automatisée disponibles. Certaines entreprises ont beaucoup de succès avec les équipements pick-to-light ou pick-to-voix. Avec pick-to-light, les préparateurs scannent un code-barres de commande et la quantité et l'emplacement de l'article s'allument. Pick-to-voice guide le préparateur et fournit une confirmation via un casque. Aujourd'hui, les technologies de réalité augmentée permettent des avancées telles que les lunettes pick-via-smart, qui affichent l'emplacement et la quantité d'un article numériquement via un casque portable. Ils fournissent des instructions vocales et la possibilité de numériser directement avec le casque, ce qui permet au travailleur d'utiliser ses deux mains et de maximiser l'efficacité avec moins de touches.
-
Mettre en œuvre des technologies intelligentes. Les technologies IoT peuvent aider à fournir des inventaires en temps réel, tout en faisant progresser la technologie des appareils portables comme les lunettes intelligentes, il est plus facile de suivre les mouvements des stocks et de s'assurer que le bon nombre est là pour commencer. Cela permet d'économiser du temps au préparateur et de la frustration de rechercher des articles qui ne sont pas là.
-
Explorez le potentiel des robots cueilleurs. Les robots de cueillette peuvent réellement faire la cueillette, avec la possibilité d'atteindre des étagères hautes et d'aller chercher des articles à emballer, tout en étant également équipé de capteurs qui les empêchent de se cogner contre des personnes ou des étagères.
-
Apprenez à connaître les co-bots. Les co-bots peuvent être utiles à déployer pour des tâches qui ont une certaine répétition, mais nécessitent également un certain niveau d'intervention humaine. Le co-bot peut assembler la box, par exemple, ou récupérer des objets de forme ou de poids prévisibles, comme une boîte à chaussures.
Meilleures pratiques et stratégies de préparation de commandes en entrepôt
La conception de l'entrepôt, Les méthodes et technologies de préparation de commandes vous aideront à déterminer laquelle des stratégies ci-dessous est la plus logique à mettre en œuvre pour améliorer vos processus de préparation de commandes.
Commencez avec un objectif clair sur ce que vous voulez améliorer et comment vous allez le mesurer, puis sélectionnez les conseils qui ont le plus de sens.
-
Demandez aux personnes qui travaillent dans l'entrepôt où se trouvent les goulots d'étranglement. N'oubliez pas les nombreuses personnes qui soutiennent souvent vos processus, y compris les administrateurs de bureau, opérateurs d'équipement et autres.
-
Ne basez pas les objectifs de préparation de commandes sur des moyennes. La saisonnalité et les tendances économiques affecteront grandement la façon dont les stocks entrent et sortent de l'entrepôt. Regarde les pics et les creux, appliquer des statistiques et utiliser des algorithmes pour déterminer des objectifs raisonnables.
-
Suivez la productivité des préparateurs. Connaître les niveaux de productivité permet au responsable de l'entrepôt de concevoir des quarts de travail en fonction de la meilleure façon de répartir le travail. Regardez les choix moyens par personne-heure, ainsi que l'inverse, heures-personnes moyennes par prélèvement. Le travail moyen par commande est alors le nombre moyen de lignes de prélèvement par commande multiplié par le nombre moyen d'heures-personnes par prélèvement.
-
Mesurez et améliorez le temps de cycle de commande total ou le temps de cycle de commande interne. La préparation des commandes est une grande partie du calcul du temps total nécessaire pour traiter une commande. Le suivi de ce numéro fournit une mesure de l'efficacité de la cueillette.
-
Examinez la précision du décompte des stocks par emplacement et sélectionnez les défauts d'emplacement (tels que les ruptures de stock/les commandes en souffrance). Cela indique qu'il n'y a pas une quantité suffisante à l'emplacement désigné.
-
Mesurez le taux de remplissage (par ligne et commandes) pour comparer les articles expédiés ce jour-là au nombre total d'articles commandés ce jour-là. Le taux de remplissage est un bon moyen de s'assurer que les opérations de l'entrepôt répondent à la demande des clients et est généralement calculé quotidiennement.
-
Mesurez la précision de la préparation des commandes. La précision de la préparation des commandes est la troisième des références les plus importantes pour les entrepôts dans le rapport d'analyse comparative de DC Measures de 2020. Une faible précision de préparation des commandes indique un besoin de processus plus efficaces, de meilleures normes de contrôle, une formation plus approfondie et plus encore.
-
N'oubliez pas les KPI qui mesurent la productivité des employés. Il s'agit notamment des lignes expédiées prélevées à l'heure, lignes expédiées par heures directes, lignes expédiées par nombre total d'heures de centre de distribution (DC), nombre total annuel d'heures DC/coût total de DC et coût DC par main-d'œuvre totale utilisée.
-
Ne sélectionnez pas plus de six repères, ciblant des métriques qui aideront à gérer l'entrepôt plus efficacement et à comparer l'efficacité de plusieurs installations.
-
Passez en revue votre espace d'entrepôt chaque fois que vous effectuez votre décompte physique. Un entrepôt de biens de grande consommation devra être mis à jour au moins tous les cinq ans, à mesure que les gammes de produits, les appétits des consommateurs et les forces économiques plus larges changent tous. Ne pas faire évoluer la conception de l'entrepôt entravera les stratégies de préparation des commandes et les améliorations.
-
Pratiquez le comptage cyclique pour éliminer la complexité et le gaspillage des SKU.
-
Des techniques telles que l'analyse d'inventaire ABC (dont il existe différents types) permettent aux entreprises de classer et d'organiser les SKU et de supprimer ou de déplacer les produits qui encombrent leurs opérations.
-
Regardez au-delà du classement des SKU uniquement par volume en dollars, mais aussi comment chaque SKU consomme des ressources comme la main-d'œuvre et l'espace. Classer les SKU en fonction du nombre de fois où ils ont été sélectionnés au cours d'un certain intervalle, rentabilité, ou difficulté de fabrication, par exemple.
-
Mettre en œuvre quelques principes Lean. Effectuez régulièrement des visites Gemba - en passant du temps à observer les processus de l'entrepôt et à vraiment comprendre comment ils sont exécutés - pour identifier les inefficacités dans l'installation. Les entreprises peuvent également mettre en œuvre des techniques de poka-yolk, où ils mettent leurs opérations à l'épreuve des erreurs et recherchent des moyens d'éviter les erreurs involontaires. Un exemple ici consiste à examiner comment le cross-docking peut améliorer le flux dans l'entrepôt.
Conseils pour la préparation des commandes en entrepôt
Une fois que le personnel de l'entrepôt sait où l'entreprise concentrera ses efforts, il peut commencer à mettre en œuvre les conseils ci-dessous pour augmenter l'efficacité et la précision et améliorer la sécurité des travailleurs.
-
Stockez ensemble les SKU populaires. La densité de sélection peut être augmentée, au moins localement, en stockant ensemble les SKU les plus populaires. Puis, les préparateurs de commandes peuvent faire plus de choix dans une petite zone, réduire la quantité d'espace qu'ils doivent couvrir et augmenter la productivité.
-
Portez une attention particulière à la répartition des produits. Le rainurage fait référence au placement soigneux des caisses individuelles dans l'entrepôt, de telle sorte que des types d'inventaire similaires soient stockés ensemble. Ils peuvent être regroupés par taille physique, articles souvent commandés ensemble, saisonnalité et plus encore. En insérant correctement le produit, les organisations peuvent réaliser jusqu'à 30 % d'économies de main-d'œuvre et assurer également une meilleure ergonomie dans l'entrepôt, Supply Chain Secrets dit. Fente selon le volume et le mouvement et revisite la stratégie une à deux fois par an. Un WMS peut aider à identifier les stratégies de positionnement appropriées et il existe de nombreux algorithmes qui peuvent aider ici.
-
Lot de commandes sur une seule ligne. Les commandes sur une seule ligne sont des commandes client pour un seul article. Pour cette raison, ils ne nécessiteront pas de tri à la fin d'un chemin de sélection et vous pouvez gagner en efficacité en demandant à un préparateur d'en obtenir autant que possible en un seul voyage.
-
Équilibrer le réapprovisionnement et la cueillette pour s'assurer que les articles sont là. Supply Chain Secrets dit qu'en règle générale, un réapprovisionnement pour cinq cueilleurs, mais que cela dépend des modèles particuliers de flux. Parfois, les entrepôts commettent l'erreur de ne mesurer les produits que par le chiffre d'affaires, quand ils doivent regarder le mouvement du produit, en tenant compte du volume et des ventes.
-
Assurez-vous que les bons documents sont associés à la bonne commande. Un cinquième du temps d'un sélectionneur d'entrepôt sert à s'assurer que les documents sont corrects, par Georgia Tech. Cela peut être grandement facilité par la mise en œuvre de scanners RF, qui automatisent le processus et assurent l'exactitude en imprimant le bordereau d'expédition de la commande.
-
Structurez les listes de sélection pour un emballage efficace. Réfléchissez à la meilleure façon dont les articles s'adapteront au mieux à la boîte dans laquelle ils seront expédiés. Un WMS peut séquencer les prélèvements dans une liste de sélection afin que les gros articles soient prélevés en premier, par exemple.
-
Maximiser la densité de coups. Une façon de le faire est d'augmenter la densité des pics, minimisant la distance entre les prélèvements pour augmenter le nombre de prélèvements par emplacement et ainsi augmenter la productivité.
-
Ne mélangez pas plusieurs SKU dans les mêmes emplacements de bac. De nombreux entrepôts ont encore un emplacement de bac qui est lié uniquement à un niveau d'étagère contenant jusqu'à dix SKU différents. Cela oblige l'employé à rechercher le bon article dans plusieurs produits.
-
Essayez de minimiser les contacts avec les marchandises. Dans la plupart des entrepôts, sept à huit personnes de l'entrée à la sortie à la gestion de l'entrepôt touchent un article, mais les entreprises les plus performantes n'auront que trois à quatre contacts. Une façon de minimiser les contacts est que les sélecteurs choisissent les articles et les mettent directement dans la boîte d'expédition, pas des bacs en plastique sur un chariot.
-
Intégrez les mesures de poids avec WMS. Les entreprises qui expédient des articles volumineux et lourds peuvent améliorer la précision de la préparation des commandes en liant les informations sur le poids de l'article à la liste de sélection. Si le choix est, par exemple, une unité courte, le système avertira automatiquement le travailleur que le poids est trop faible et lui demandera d'ajouter une unité supplémentaire.
-
Choisissez parmi la pile au sol. Une stratégie de positionnement des produits consiste à laisser les sélecteurs prélever des articles à rotation élevée dans des cartons sur des palettes au sol à l'aide d'un transpalette ou d'un transpalette. Cela peut être plus efficace que de conserver ces articles à vente rapide sur des rayonnages à palettes hautes.
-
Les gens devraient choisir en utilisant des carrousels horizontaux au lieu d'ascenseurs verticaux. De multiples efforts d'analyse comparative au fil des ans ont démontré qu'il en coûte plus cher de choisir verticalement qu'horizontalement. Mais l'utilisation de la capacité de l'entrepôt exige que les choses soient également stockées verticalement. Choisissez les articles à vitesse la plus lente dans le stockage vertical et gardez les articles à grande vitesse au niveau du sol.
-
Choisissez parmi une zone de sélection avant ou rapide. Les entreprises conçoivent des zones de leur entrepôt pour abriter des SKU populaires qui se trouvent au rez-de-chaussée et sont réapprovisionnés par des stocks provenant d'autres zones du DC. Georgia Tech affirme que la zone de sélection avant la plus courante est le rayonnage à palettes du rez-de-chaussée qui est réapprovisionné en déplaçant les palettes vers le bas des niveaux supérieurs. D'autres exemples sont un rack d'écoulement de carton réapprovisionné à partir du stockage en vrac, ou un équipement spécialisé comme un carrousel ou un cadre en A qui est stocké ailleurs.
Prendre des mesures pour former et prendre soin des personnes qui travaillent dans l'entrepôt est un autre élément essentiel pour garantir l'efficacité, préparation de commandes précise et rentable.
-
Assurez-vous que le raisonnement derrière la stratégie de gestion d'entrepôt et pourquoi c'est important pour l'entreprise est compris par tout le personnel de l'entrepôt, pas seulement les gestionnaires. Un excellent exemple de la raison pour laquelle cela est important vient de SI Systems, qui souligne que lorsque de nombreuses entreprises mettent en œuvre la vérification par double code-barres, où l'opérateur scanne le SKU du produit puis la palette, pour améliorer la précision. Cependant, l'opérateur scanne souvent la palette en double car c'est plus rapide. L'employé le fait parce qu'il veut atteindre les niveaux de productivité ou de débit et ne réalise pas pourquoi la numérisation des deux est cruciale pour la précision des stocks. Vous devez mener un processus de formation formel avec les membres de l'équipe et expliquer la justification commerciale de chaque partie d'un processus.
-
Utilisez des mesures réelles pour définir des normes de performance réalistes pour les employés d'entrepôt. Utiliser des métriques telles que les lignes de commandes prélevées par heure et le coût de prélèvement pour chaque ligne de commande et chercher à les améliorer en donnant aux sélecteurs les bonnes technologies qui faciliteront une efficacité et une précision accrues, tels que le pick-to-light et le pick-to-voice.
-
Favoriser la coopération. Un tableau de bord qualité ou un centre de contrôle peut aider à surveiller les performances globales de l'entrepôt pour récompenser et encourager les équipes, mais cherchez également à mettre en évidence les gains individuels des employés. Affichez les statistiques des plus performants et incitez-les à une forte productivité et à des performances de sécurité.
-
Travailler pour réduire les heures supplémentaires. Comparez les heures globales à la sortie et regardez les lignes de commande sélectionnées par heure de main-d'œuvre, par exemple, pour évaluer l'efficacité du travail. Prendre en compte les heures normales de travail par rapport aux heures supplémentaires, lignes prélevées par jour et nombre de cartons, chacunes ou palettes prélevées par période. Comparez cette période sur une période. Si ces chiffres sont faibles, mais les heures supplémentaires sont élevées, j'ai trouvé pourquoi.
-
Prenez des mesures pour rendre le lieu de travail plus sûr et conforme aux normes OSHA. Les meilleures opérations d'entrepôt ont des programmes formels de formation à la sécurité et une formation continue. Placez les produits dans ce qu'on appelle la «zone dorée» pour assurer une bonne santé ergonomique. Marquez clairement les allées et les zones de travail avec des marqueurs de sécurité et gardez-les exempts de débris et de dangers. S'assurer que tous les EPI appropriés sont portés par les employés de l'entrepôt à tout moment, y compris les casques, lunettes, des gants, masques, uniformes appropriés et plus encore.
-
Examiner et affiner les processus régulièrement. À mesure que les stratégies de produits évoluent, assurez-vous que la stratégie de l'entrepôt le fait aussi. Les défis de la chaîne d'approvisionnement et les efforts visant à accroître la résilience de la chaîne d'approvisionnement remettront en question de nombreux principes de gestion des stocks juste à temps qui ont guidé les opérations des entrepôts pendant des années. Dans de nombreux cas, plus d'espace sera nécessaire et le stock peut être conservé pendant de plus longues périodes pour être prêt pour les surtensions et les pénuries. En effet, la demande d'espace d'entrepôt est élevée - Le Wall Street Journal a rapporté que l'activité immobilière industrielle a augmenté de 43% d'avril à mai 2020, avec une demande d'entrepôts de plus de 100, 000 pieds carrés étant le plus fort.
Optimisez la préparation des commandes avec le logiciel de gestion d'entrepôt
Considérez la commande du client comme une liste de courses que le préparateur doit remplir, à chaque entrée de la liste (appelées lignes de commande) notant l'article et la quantité. Idéalement, un système de gestion d'entrepôt est en place pour vérifier l'inventaire disponible et où le trouver, ainsi que de réorganiser les commandes dans une liste de sélection qui tient compte de la disposition de l'entrepôt pour augmenter la vitesse. Le nombre de lignes de prélèvement peut être une indication du nombre de déplacements que le travailleur devra parcourir dans l'entrepôt pour obtenir les articles nécessaires aux commandes.
Les entreprises peuvent se tourner vers les systèmes de gestion d'entrepôt (WMS) pour les aider à gérer les processus entrants et sortants de leurs entrepôts et gagner en visibilité sur tous les SKU stockés et leur emplacement. La fonctionnalité WMS s'appuie sur celle d'une solution de gestion des stocks, et a également des capacités pour aider à la stratégie de stockage et à la gestion de la main-d'œuvre. Le WMS fournit des détails sur tous les articles dans l'entrepôt - dimensions physiques, comment c'est emballé, où il est stocké et le chemin le plus efficace pour y accéder.
Un WMS prend en charge la prise de rendez-vous, recevoir, assurance qualité, ranger, suivi de localisation, gestion des bons de travail, cueillette, emballage et consolidation et expédition. Le WMS transforme une commande client en liste de sélection et suit l'assemblage de la commande. Le WMS peut également gérer les processus entrants dans un entrepôt, indiquant où l'inventaire doit être stocké, suivi de la productivité des travailleurs, s'assurer que les commandes respectent les calendriers d'expédition et plus encore. Il peut également se connecter aux systèmes de gestion des commandes et ERP. Spécifiquement, pour la fonction picking, un WMS robuste peut prendre en charge le pick-to-light, Opérations dirigées par RF, planification du travail, SKU slotting et bien plus encore.
Le bon WMS évoluera au fur et à mesure que de nouvelles fonctionnalités seront nécessaires et s'adaptera au fur et à mesure que les processus changent. Alors que le bâtiment lui-même peut rester statique, les processus et les technologies d'une entreprise ne doivent pas être gravés dans le marbre. En regardant constamment les systèmes et la façon dont les gens les utilisent pour accomplir leur travail, la gestion des entrepôts peut être constamment améliorée, aider les employés à faire leur travail plus efficacement et s'assurer que les clients continuent d'acheter et de faire confiance à votre entreprise.
Entreprise
- 11 meilleurs régimes de retraite :avantages et inconvénients
- Quand acheter une action et quand vendre une action :5 conseils
- Prévision d'inventaire :Types,
- Inventaire physique :étapes,
- Gestion des stocks au détail :qu'est-ce que c'est ?
- 35 métriques de commerce électronique avec des formules, Repères et conseils
- 51 conseils de gestion d'entrepôt pour votre entreprise
- Guide ultime de la préparation des commandes :types, Méthodes et astuces
- Les meilleurs conseils, Des trucs, et outils pour travailler à distance
-
Meilleurs conseils et informations utiles sur la façon de trader la crypto-monnaie
Avant de plonger tête baissée dans le trading Bitcoin, il existe de nombreux conseils essentiels dont vous avez besoin si vous prévoyez une conduite presque en douceur dans votre nouvelle entreprise. ...
-
Est-il risqué d'échanger des Altcoins ? – Bonnes pratiques et informations utiles
Dans une large mesure, cette pandémie actuelle a ravagé de nombreuses entreprises et secteurs financiers, y compris le marché des crypto-monnaies. Bien que Bitcoin ait dominé le marché des crypto-monn...